On 23th, April, we received an inquiry from Bolivia. This client sought for 400 pieces 180°elbows in carbon steel with simple drawing attached.
Elbows are within our products. Thus we offered our competitive quotation based on the drawing. Two months later, the customer showed us more accurate drawing, together with many photos showing the details of the elbow that they wanted. We inspected all the information offered updated quotation fulfilling customer’s requirements.
After reviewing our quotation, the client placed the order. And after reviewing our sample elbow, we manufactured in quantity.
We took very detailed photos of the sample to make sure that’s what our client want.
ITEM | Description | Description | Type | Conenection | Size | Pressure | Material | Standard | Quanitity | Unit |
1 | STEEL ELBOW 180-DN 65 SCH160 ASTM A234 WPB | 180 DEG ELBOW | SMLS | BW | DN65 2-1/2″ | SCH160 | ASTM A234WPB | ASME B16.9 | 200 | EA |
Sample inspection photos
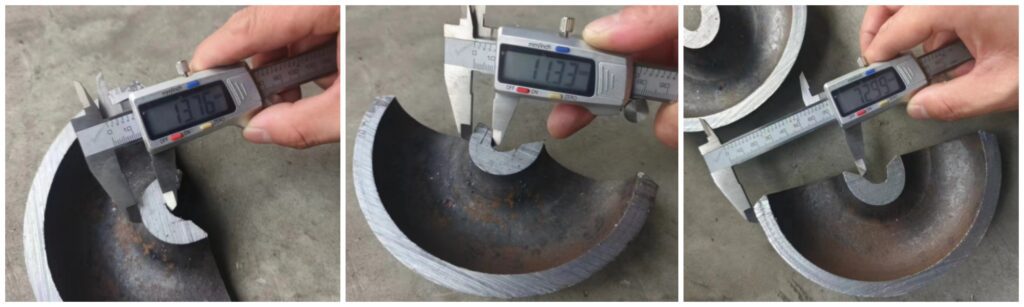
ASTM A234 WPB Elbow Specification
ASTM A234 WPB Elbow refers to an elbow pipe fitting made from carbon steel that complies with the ASTM A234 standard and has a WPB material grade designation. The A234 specification covers wrought carbon steel and alloy steel fittings that are intended for use in pressure piping systems. The WPB grade specifically refers to a material that is commonly used for seamless and welded butt-welding fittings.
Butt Weld Elbow is a commonly used pipe fitting, usually used to change the direction of the pipe. According to the angle of the elbow, there are three common types of butt weld elbows: 45 degrees, 90 degrees and 180 degrees.
The 45 degree butt weld elbow is an elbow used to change the direction of the pipe. The bending angle is 45 degrees, which is used to offset the direction of the pipe by 45 degrees.
The 90 degree butt weld elbow is used to change the direction of the pipe by 90 degrees, that is, to form a right angle. This type of elbow is common in pipe systems that require large turns.
The 180 degree butt weld elbow is usually used when the direction of the pipe is completely reversed, forming a U-shaped bend. It completely reverses the flow direction of the pipe and returns to the starting position.
Specification: | ASTM A234 WPB Elbow |
Degree | 45 deg,90 deg,180 deg |
Size: | Normal Pipe Size (NPS) 1⁄₂ to Normal Pipe Size (NPS) 48” |
Standard | EN, ISO, DIN, JIS, NPT |
Connection Type | Threaded/ Clamp End / End Bell / Weld/ Flange/ |
Type: | Butt Weld (BW), Seamless (SMLS) Welded |
Thickness: | SCH10, SCH20, SCH30, STD SCH40, SCH60, XS, SCH80., SCH100, |
Type Of Dimension: | BS1640, EN 10253 – 4, DIN 2605, JIS B2312, ANSI B16.9, MSS SP-75, ANSI B16.28, MSS-SP-43 Type A, MSS-SP-43 Type B, JIS B2313 |
ASTM A234 WPB Butt Weld Fittings Chemical Composition
CHEMICAL | LIMITS | C | Mn | P | S | Si | Cr | Mo | Ni | Cu | Cb | V |
ASTM A234 WPB | MIN | 0.29 | 0.10 | |||||||||
MAX | 0.30 | 1.06 | 0.050 | 0.058 | 0.40 | 0.15 | 0.40 | 0.40 | / | 0.08 |
ASTM A234 WPB Butt Weld Fittings Mechanical Property
MATERIAL | T.S (MPA) | Y.S (MPA) | EL % | R/A % | HARDNESS |
ASTM A234 WPB | 415 min | 240 min | 22 min | 30 min | 197 max |
180 Degree Elbow Dimension
Nominal Size | Outside Diameter at Bevel | Center to Center | Back to Face | |||
180° Returns | ||||||
DN | NPS | OD | O | K | ||
LR | SR | LR | SR | |||
15 | 1/2 | 21.3 | 76 | 48 | ||
20 | 3/4 | 26.7 | 76 | 51 | ||
25 | 1 | 33.4 | 76 | 51 | 56 | 41 |
32 | 1 1/4 | 42.2 | 95 | 64 | 70 | 52 |
40 | 1 1/2 | 48.3 | 114 | 76 | 83 | 62 |
50 | 2 | 60.3 | 152 | 102 | 106 | 81 |
65 | 2 1/2 | 73 | 190 | 127 | 132 | 100 |
80 | 3 | 88.9 | 229 | 152 | 159 | 121 |
90 | 3 1/2 | 101.6 | 267 | 178 | 184 | 140 |
100 | 4 | 114.3 | 305 | 203 | 210 | 159 |
125 | 5 | 141.3 | 381 | 254 | 262 | 197 |
150 | 6 | 168.3 | 457 | 305 | 313 | 237 |
200 | 8 | 219.1 | 610 | 406 | 414 | 313 |
250 | 10 | 273 | 508 | 518 | 391 | |
300 | 12 | 323.8 | 914 | 609 | 619 | 467 |
350 | 14 | 355.6 | 1067 | 711 | 711 | 533 |
400 | 16 | 406.4 | 1219 | 813 | 813 | 610 |
450 | 18 | 457 | 1372 | 914 | 914 | 686 |
500 | 20 | 508 | 1524 | 1016 | 1016 | 762 |
550 | 22 | 559 | 1676 | 1118 | 1118 | 838 |
600 | 24 | 610 | 1829 | 1219 | 1219 | 914 |
650 | 26 | 660 | ||||
700 | 28 | 711 | ||||
750 | 30 | 762 | ||||
800 | 32 | 813 | ||||
850 | 34 | 864 | ||||
900 | 36 | 914 | ||||
950 | 38 | 965 | ||||
1000 | 40 | 1016 | ||||
1050 | 42 | 1067 | ||||
1100 | 44 | 1118 | ||||
1150 | 46 | 1168 | ||||
1200 | 48 | 1219 |
Tolerances for Butt-Weld Fittings
TOLERANCES FOR BW FITTINGS | |||||||||||||
Nominal Size | All Fittings | 45°&90° Elbows & Tees, Crosses | 180° Returns | Caps | Reducers & Lap Joint Stub Ends | Lap Joint Stub Ends | |||||||
DN | NPS | OD 3) 4) | ID 3) | A B C M | A B | K | U | E, E1 | H F | R | t | ||
15-65 | 1/2 -21/2 | +1.6 -0.8 | ± 0.8 | ± 2 | ± 3 | ± 6 | ± 6 | ± 1 | ± 3 | ± 2 | 0 -1 | 0 -1 | +1.6 0 |
80-90 | 3-31/2 | ± 1.6 | ± 1.6 | ± 2 | ± 3 | ± 6 | ± 6 | ± 1 | ± 3 | ± 2 | 0 -1 | 0 -1 | +1.6 0 |
100 | 4 | ± 1.6 | ± 1.6 | ± 2 | ± 3 | ± 6 | ± 6 | ± 1 | ± 3 | ± 2 | 0 -1 | 0 -2 | +1.6 0 |
125-200 | 5-8 | +2.4 -1.6 | ± 1.6 | ± 2 | ± 3 | ± 6 | ± 6 | ± 1 | ± 6 | ± 2 | 0 -1 | 0 -2 | +1.6 0 |
250-450 | 10-18 | +4.0 -3.2 | ± 3.2 | ± 2 | ± 3 | ± 10 | ± 6 | ± 2 | ± 6 | ± 2 | 0 -2 | 0 -2 | +3.2 0 |
500-600 | 20-24 | +6.4 -4.8 | ± 4.8 | ± 2 | ± 3 | ± 10 | ± 6 | ± 2 | ± 6 | ± 2 | 0 -2 | 0 -2 | +3.2 0 |
650-750 | 26-30 | +6.4 -4.8 | ± 4.8 | ± 3 | ± 6 | — | — | — | ± 10 | ± 5 | — | — | — |
800-1200 | 32-48 | +6.4 -4.8 | ± 4.8 | ± 5 | ± 6 | — | — | — | ± 10 | ± 5 | — | — | — |
1300-1500 | 52-60 | +6.4 -4.8 | ± 4.8 | ± 5 | — | — | — | — | — | — | — | — | — |
1600-1700 | 64-68 | +6.4 -4.8 | ± 4.8 | ± 5 | — | — | — | — | — | — | — | — | — |
1800-2000 | 72-80 | +6.4 -4.8 | ± 4.8 | ± 5 | — | — | — | — | — | — | — | — | — |
Inspection and Testing
Visual Inspection: To ensure there are no surface defects, cracks, or deformation.
Dimensional Inspection: Verifying the elbow’s dimensions, wall thickness, and radius, ensuring it meets the required specifications.
NDT (Non-Destructive Testing): Methods like X-ray, ultrasonic testing (UT), or magnetic particle testing (MPT) may be used to check for internal flaws or weld defects, particularly for critical applications.
Hydrostatic Testing: Performed to ensure that the elbow can withstand the pressure it will encounter during service without leaking.
ASTM A234 WPB Elbow Application
1. Oil and Gas Industry
2. Chemical Processing
3. Power Plants
4. Water Treatment Plants
5. Heating and Ventilation Systems (HVAC)
6. Marine and Shipbuilding
7. Industrial Manufacturing and Construction
8. Food and Beverage Industry
9. Pharmaceutical Industry